How Does the Electronic Accelerator of a DRIVE-BY-WIRE Car Work?
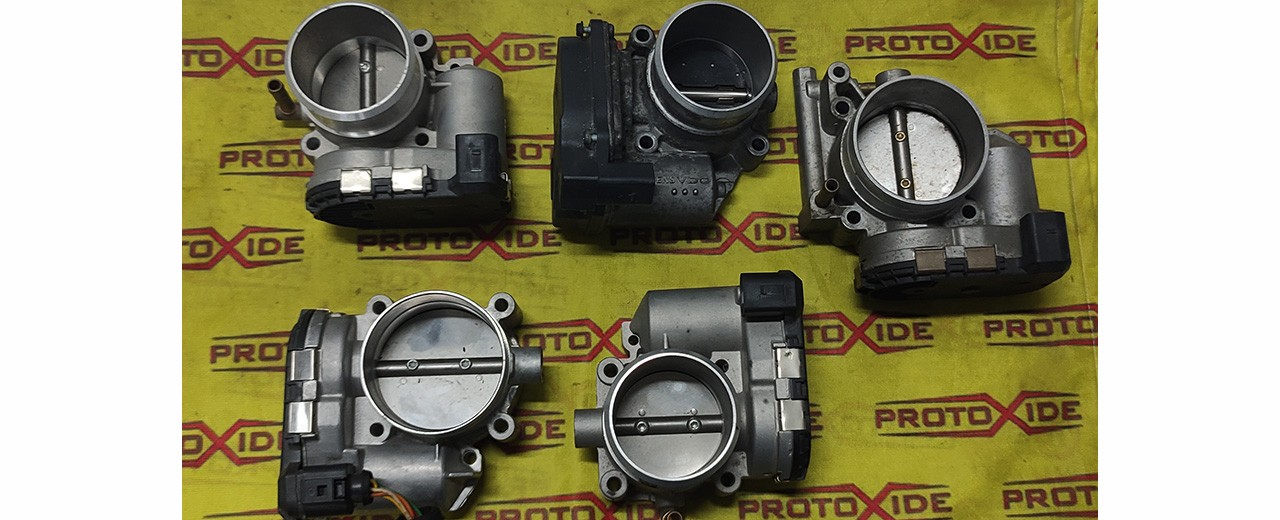
In the modern era of automotive engines, the drive-by-wire system has revolutionized the way vehicles respond to accelerator inputs. But how exactly does an electronic accelerator in a car work? This article explores the technological details behind how the electronic accelerator in modern cars works, providing an overview of the drive-by-wire system.
The Drive-By-Wire System
The drive-by-wire system eliminates the traditional mechanical connection between the accelerator pedal and the throttle body. Instead, it uses electronic sensors to communicate with the vehicle's electronic control unit (ECU). The accelerator pedal is designed with two independent potentiometer strips inside, which convert the position of the pedal into variable electrical signals, known as demand signals.
How Ask Signals Work
These request signals are essential to tell the ECU how much the driver wants to accelerate. A typical signal in automotive specification varies from about 0.4 volts to 2.5 volts, while the other potentiometer operates between 2.5 volts and 5 volts. This signal differentiation is essential to ensure precise and safe control of the accelerator. The variation of the signals avoids the emission of identical signals, or easy changes in the event of a fault, thus facilitating a double check of the ECU to ensure the correctness of the system and the consequent difficulty in manipulating it.
The Role of the ECU
The ECU interprets the request signals and, through the engine control unit, sends commands to an electric motor that regulates the opening of the electronic throttle. If wheel slippage occurs or if the turbo pressure becomes excessive, the ECU can intervene to limit the opening of the throttle, ensuring the stability of the vehicle and protecting it from possible damage.
Many times especially after a mapping not done properly you can have the feeling that the car is not going as it should, without necessarily showing signs of failure on the dashboard, this usually around 3000 rpm. This can also happen in some cases, that the ECU keeps the accelerator slightly closed with the accelerator pedal fully pressed, to limit the amount of torque that the engine can generate.
Feedback Sensors
In addition to the pedal potentiometers, two more potentiometers are connected to the electronic throttle. These feedback sensors provide the ECU with real data on the throttle position, allowing precise control synchronized with the demand signals.
System Security and Reliability
The dual control of the request and feedback signals ensures that in the event of a malfunction, the system can prevent critical errors. However, given the complexity of the system, it is crucial that any modification to the drive-by-wire system is carried out carefully to avoid serious consequences or accidents due to the sensitive role that this component plays.
In conclusion, the electronic accelerator of a modern car not only improves the precision of control but also the efficiency and safety of the vehicle. Drive-by-wire technology represents the future of acceleration management in automotive engines, promising continuous innovation and advanced performance.
ProtoXide Unichip Control Unit Solutions
ProtoXide sells electronic control units that can be connected to the original control unit to manage all the signals coming from the accelerator and consequently independently move the electronic throttle according to our strategies.
These Unichip control units can also be used to directly manage the throttle and have numerous other functions that manage a complete engine.